5 Essential Quality Tools Every CQPA Should Master
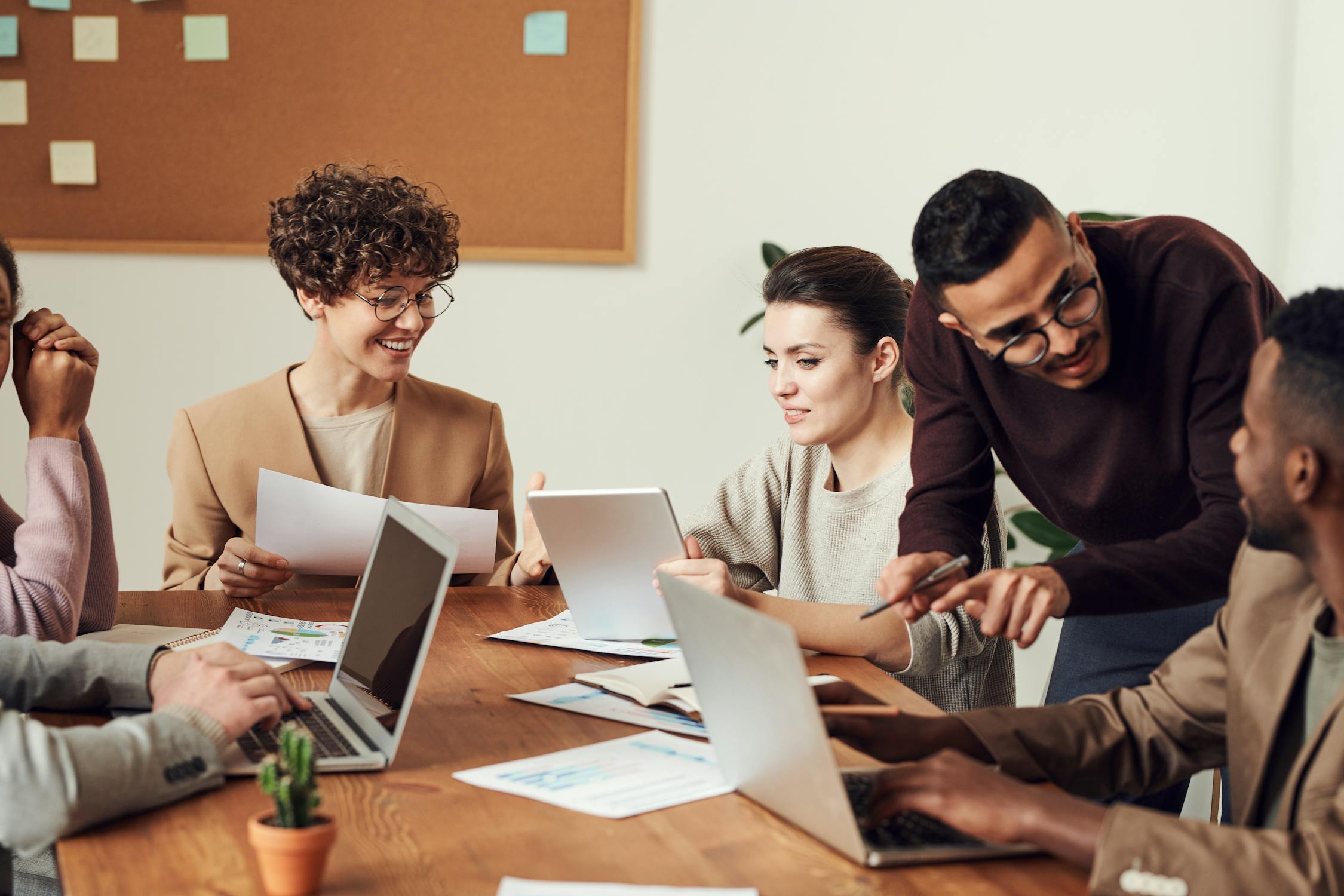
John Lee
Published on May 15, 2025 · 12 min read
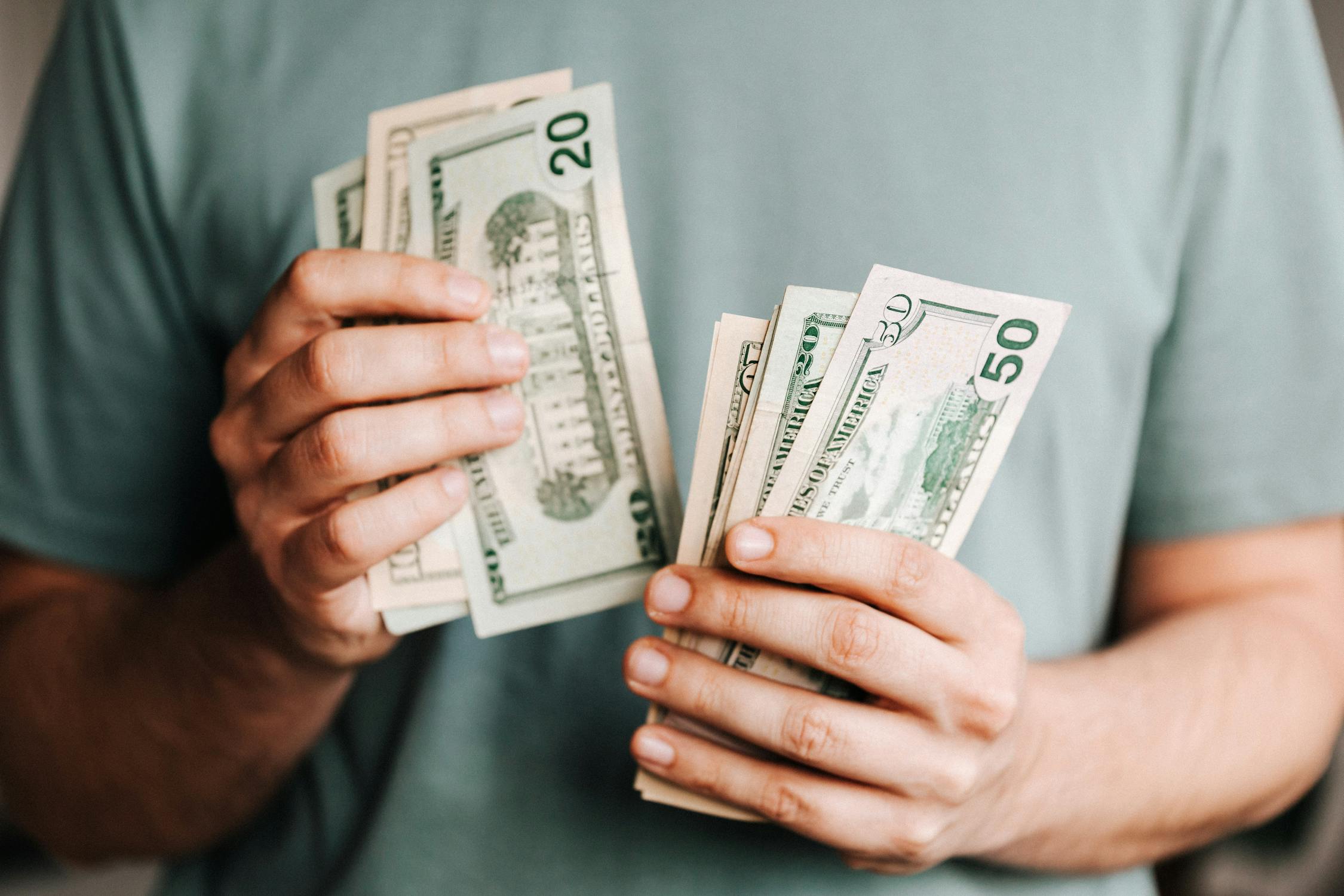
Quality improvement is at the heart of what Certified Quality Process Analysts (CQPAs) do every day. To excel in this role, you need a solid understanding of various quality tools and techniques. In this article, we'll explore five essential quality tools that every CQPA should master to effectively analyze, improve, and control processes.
1. Process Mapping and Flowcharting
Process mapping is a fundamental technique for visualizing workflows, identifying bottlenecks, and understanding how processes function. As a CQPA, your ability to create clear, accurate process maps is invaluable for process analysis and improvement initiatives.
Key Benefits:
- Provides a visual representation of process steps and their relationships
- Helps identify redundancies, delays, and non-value-adding activities
- Facilitates communication and common understanding among team members
- Serves as a baseline for process improvement efforts
How to Use Process Mapping Effectively:
- Define the process scope - Clearly identify the beginning and end points of the process you're mapping, including key inputs and outputs.
- Gather the right team - Include people who actually perform the work to ensure accuracy.
- Use standard symbols - Follow established flowcharting conventions (rectangles for activities, diamonds for decisions, etc.).
- Validate with stakeholders - Ensure the map accurately represents the current process before using it for analysis.
- Analyze for improvement - Look for loops, delays, redundancies, and handoffs that might indicate opportunities for streamlining.
Process maps come in various formats, including high-level SIPOC diagrams (Suppliers, Inputs, Process, Outputs, Customers), swimlane diagrams that show responsibilities across departments, and detailed flowcharts that capture every step and decision point.
2. Cause-and-Effect Analysis (Fishbone Diagrams)
Also known as Ishikawa or fishbone diagrams, cause-and-effect analysis is a powerful tool for identifying potential causes of problems or effects. This structured approach helps teams brainstorm and categorize possible causes, preventing them from jumping to conclusions or focusing on symptoms rather than root causes.
Key Benefits:
- Encourages systematic thinking about problem causes
- Organizes ideas into logical categories
- Helps separate symptoms from underlying causes
- Creates a visual record of the analysis for future reference
Standard Categories (6 Ms):
- Manpower/People - Issues related to human factors, training, skills
- Methods - Process-related issues, procedures, techniques
- Machines/Equipment - Tool or equipment-related factors
- Materials - Issues with inputs, components, consumables
- Measurements - Data collection, metrics, monitoring issues
- Mother Nature/Environment - Factors in the physical environment
When facilitating a cause-and-effect analysis, encourage the team to dig deeper by repeatedly asking "why" (similar to the 5 Whys technique) to get beyond surface-level causes. The most powerful use of this tool comes from combining it with data collection to verify which potential causes are actually significant.
3. Pareto Analysis
Based on the Pareto Principle (often called the 80/20 rule), this analytical approach helps identify the "vital few" factors that have the greatest impact on a problem or situation. By focusing improvement efforts on these key issues, CQPAs can help organizations achieve maximum results with limited resources.
Key Benefits:
- Prioritizes improvement efforts based on impact
- Provides visual clarity on problem frequency or significance
- Helps focus limited resources where they'll have the greatest effect
- Demonstrates progress when comparing before-and-after charts
Steps to Create a Pareto Chart:
- Identify and categorize problems or causes
- Establish a measurement unit (frequency, cost, time, etc.)
- Collect and tabulate data for each category
- Sort categories from highest to lowest count
- Calculate cumulative percentages
- Create the chart with bars for each category and a cumulative percentage line
The power of Pareto analysis lies in its ability to cut through complexity and direct attention to the most impactful areas for improvement. In quality improvement projects, this tool often reveals that a small number of issues (typically 20%) are responsible for the majority (around 80%) of the problems.
4. Statistical Process Control (SPC) Charts
SPC charts are essential tools for monitoring process stability and capability over time. As a CQPA, understanding how to create, interpret, and use these charts is critical for distinguishing between common cause variation (inherent in the process) and special cause variation (requiring investigation and action).
Common Types of Control Charts:
- X-bar and R charts - For monitoring the mean and range of a variable in subgroups
- Individual and moving range (I-MR) charts - For continuous data when subgrouping isn't possible
- p charts - For monitoring proportion of defective items
- c charts - For counting the number of defects when sample size is constant
- u charts - For counting defects per unit when sample size varies
Key Elements of Control Charts:
- Central line - Represents the process average
- Upper and lower control limits - Typically set at ±3 standard deviations from the mean
- Data points - Individual measurements or subgroup statistics plotted over time
- Out-of-control signals - Patterns indicating special cause variation
Understanding control chart patterns is essential. Look for points outside control limits, runs (seven or more consecutive points on the same side of the centerline), trends (seven or more consecutive points increasing or decreasing), and other non-random patterns that suggest the process needs investigation.
5. Failure Mode and Effects Analysis (FMEA)
FMEA is a systematic, proactive approach to identifying potential failures in processes or products before they occur. This preventive tool helps quality professionals anticipate problems and implement controls to prevent them, making it an invaluable part of the CQPA toolkit.
Key Benefits:
- Identifies potential failure modes before they impact customers
- Prioritizes improvement actions based on risk
- Documents current knowledge and actions for future reference
- Reduces costs by preventing problems rather than fixing them
- Supports continuous improvement and organizational learning
FMEA Process:
- Identify potential failure modes - Ways in which the process or product might fail to meet requirements
- Determine potential effects - What would happen if each failure occurred
- Identify potential causes - What might lead to each failure
- List current controls - Existing measures to prevent or detect the failure
- Assign severity, occurrence, and detection ratings - Typically on a 1-10 scale
- Calculate Risk Priority Number (RPN) - Severity × Occurrence × Detection
- Develop action plans - For high-risk items (high RPNs)
- Implement actions and recalculate RPNs - To verify improvement
FMEA can be applied to processes (Process FMEA) or products (Design FMEA). Both approaches follow similar methodologies but focus on different aspects of the business. The structured nature of FMEA makes it particularly valuable for complex processes or critical applications where failures could have significant consequences.
Integrating These Tools in CQPA Practice
While each of these tools is powerful on its own, their true value comes from using them together as part of a comprehensive quality improvement approach. Here's how these tools might work together in a typical improvement project:
- Create a process map to understand the current state
- Use cause-and-effect analysis to identify potential problem sources
- Apply Pareto analysis to focus on the most significant issues
- Implement SPC charts to monitor process changes and verify improvements
- Conduct FMEA to prevent new problems in the redesigned process
As a CQPA, your ability to select and apply the right tools at the right time is a valuable skill. With practice, you'll develop an intuitive sense of which tools will be most effective for different situations and how to adapt them to the specific needs of your organization.
Conclusion
Mastering these five quality tools—process mapping, cause-and-effect analysis, Pareto analysis, SPC charts, and FMEA—will significantly enhance your effectiveness as a Certified Quality Process Analyst. These tools provide a structured approach to analyzing, improving, and controlling processes, which is at the heart of the CQPA role.
Remember that tools are means to an end, not the end itself. The ultimate goal is to improve processes, reduce defects, enhance customer satisfaction, and create value for your organization. Let these tools guide your thinking and support your decision-making, but always keep the bigger picture in mind.
As you prepare for the ASQ CQPA certification or seek to enhance your skills as a certified professional, focus on understanding not just how to use these tools but when and why to apply them. This deeper understanding will set you apart as a quality professional and enable you to make meaningful contributions to your organization's quality journey.
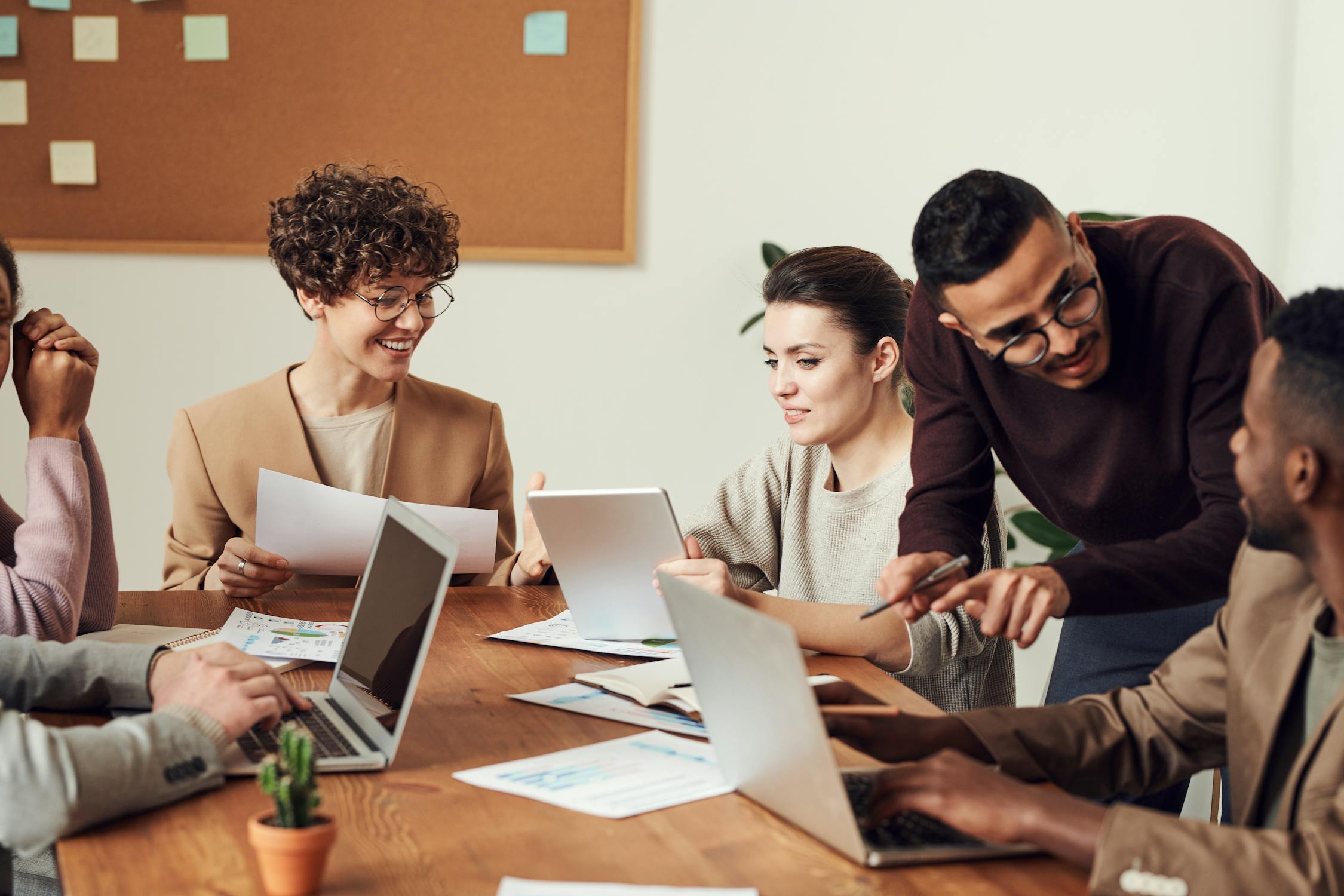
About the Author
John Lee is the Lead Instructor and Office Manager at Alpha Training & Consulting. With over 15 years of experience in quality management, John has helped hundreds of professionals achieve their ASQ certification goals. He holds multiple ASQ certifications including CQE and CSSBB.
Related Articles
Preparing for the ASQ CQPA Exam: A Comprehensive Guide
Discover proven strategies, study tips, and resource recommendations to help you prepare effectively for the ASQ CQPA certification exam.
Statistical Process Control: A Practical Approach
A beginner-friendly guide to understanding and implementing statistical process control techniques in your organization.
Ready to Master Quality Management Tools?
Enroll in our ASQ CQPA certification training to develop expert-level skills in quality process analysis and improvement.
Enroll Now - $695